Hot Air Recirculation
Significantly reduce your Grain Dryer fuel costs by using Hot Air Recirculation
Save up to 24%* of your Grain Dryer fuel costs
How Does It Work?
The Grain Dryer fuel savings come from the reduction in the amount of fuel the Dryer consumes to heat the air to dry the grain.
The cooling air, from the lower levels of the Grain Dryer, which is unsaturated and of the highest temperature, is recirculated to the hot air side of the Dryer and remixed with the heated air.
Depending on the Dryer size, 25% to 30% of the warmest air in the Dryer is moved by the recirculation fan along transfer ducts to an additional plenum and mixed with the freshly heated ambient air.
*The actual percentage savings on Dryer operating costs by using Hot Air Recirculation can be significant and will vary based on:
- Hot air and ambient air temperature
- Crop type and moisture
- Dryer model & fan speed
- Ambient conditions
Some examples of the theoretical level of Grain Dryer fuel cost savings are:
125°C hot air temperature, 15°C ambient, percentage saving 16% to 18% depending on Dryer model selected.
70°C hot air temperature, 15°C ambient, percentage saving 21% to 24% depending on Dryer model selected.
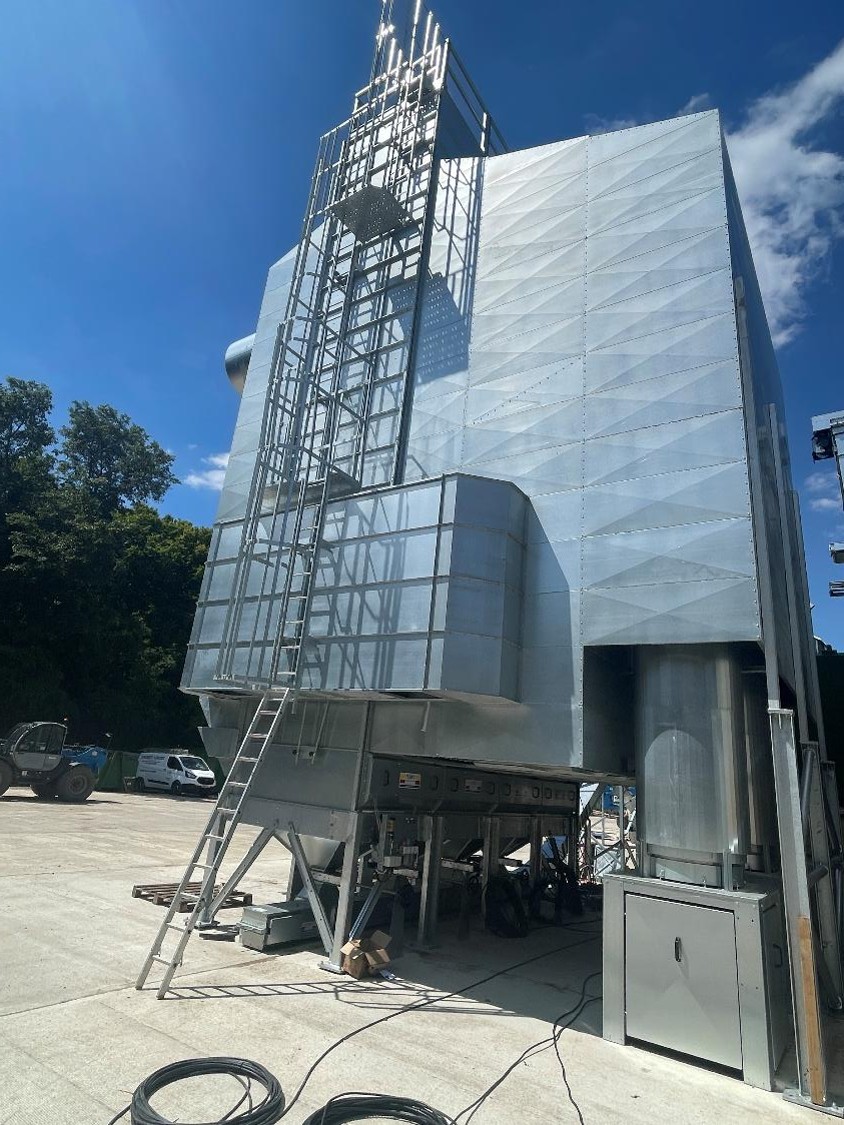
Maximise Your Operational Savings
Increase your theoretical operational cost savings up to 35% by combining Hot Air Recirculation with:
How Our Grain Sentry Moisture Control System Can Improve The Efficiency Of Your Grain Drying
The Grain Sentry Moisture Control system is used by farmers and grain stores that need to store large quantities of grain for extended periods. It helps to ensure that the grain is stored under optimal conditions, maintaining its quality and value. As a team with...
Everything You Need To Know About Perry Of Oakley Silos
We cover everything you need to know about Perry of Oakley Silos. Contact us today to discuss which silo is best for your requirements.
Why Trust Matters – 70 Years Of Engineering Excellence
Here at Perry’s, we’re the only UK company that manufactures a full range of both bulk materials handling and drying machinery. The handling equipment is capable of capacities from 8tph (agricultural specification) to 1200tph (industrial specification) and includes...